What is a Blueprint Takeoff? A Comprehensive Guide to Construction Takeoff Process
Written by Bridget Cooper
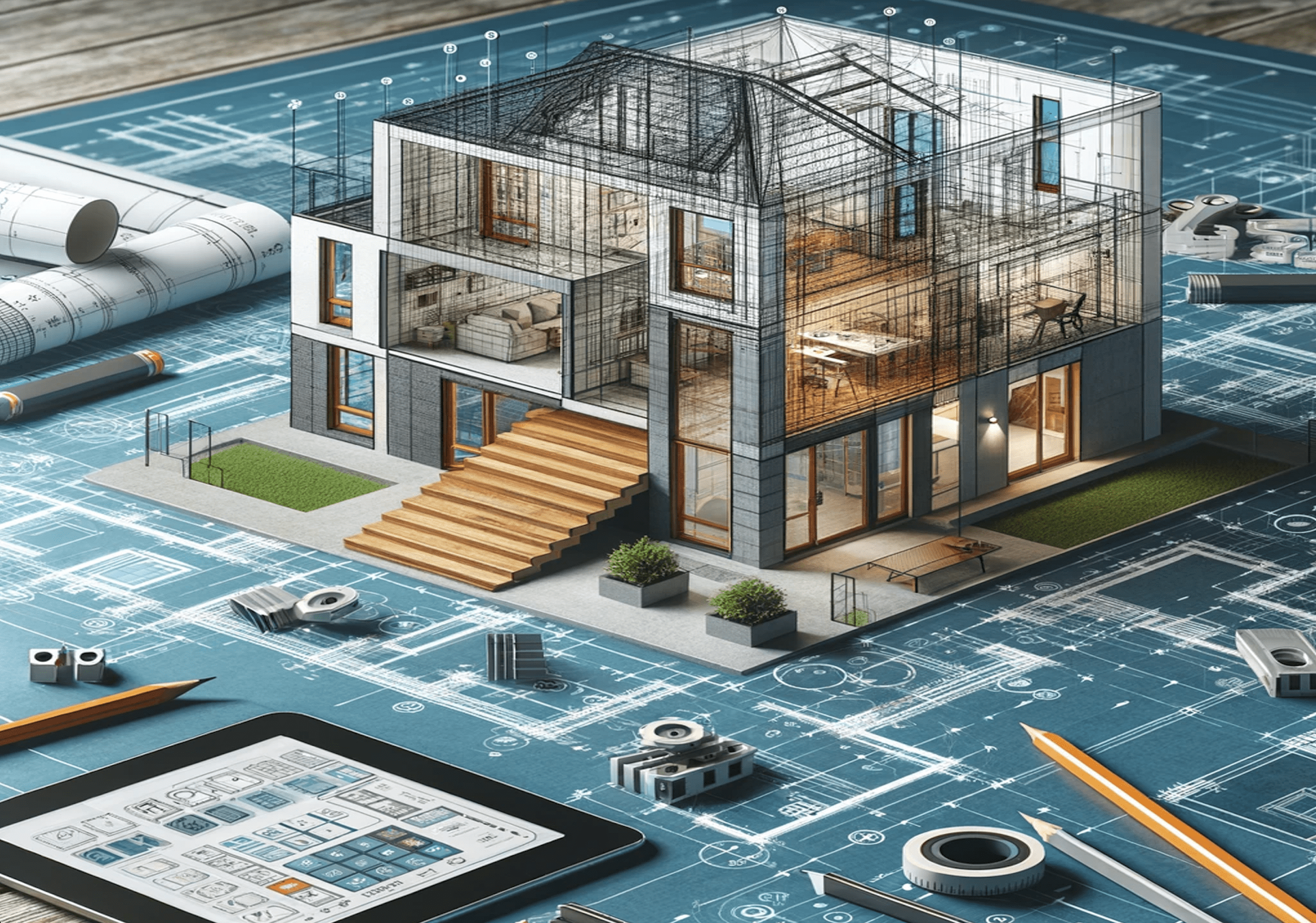
Before contractors and subcontractors bid or start a construction project, they have to know the type and number of materials the construction project will need. They can only have this information if they perform a construction takeoff. So, how is a material takeoff in construction done? In this article, you will learn how the construction takeoff process works and an example is also included.
What Does a Takeoff Mean In Construction?
A takeoff in construction, also known as material takeoff or quantity takeoff, typically consists of all the materials needed in a construction project and the estimated labor costs to install the materials needed. In simple terms, a takeoff process is where contractors determine how much materials they need to complete a construction project.
Takeoffs play a major role in construction because it gives an estimate for the project. Logically, when the square footage of a project is more, more materials and labor are needed to complete the project. So, having an accurate takeoff eliminates the possibility of contractors underbidding and then losing the money or overbidding and lose the construction job.
In addition, contractors use takeoffs for various reasons, including estimating the project costs and submitting bids. Now, let's look at each scenario in detail.
- Submitting bids: When bidding on a construction job, it's critical to understand how much of each material you will need for the entire project. This will help you determine the material costs you will include in your bid. Without this information, you may end up underbidding on the project and lose money or overbid and miss the chance to win the job. But, with an accurate takeoff, you maximize your chances of winning the bid.
- Creating estimates: By estimating the entire construction project, you will know the materials needed. There are two methods that you can use. You can give your best guess of the project costs or perform a construction takeoff. Remember, performing a takeoff guarantees a more accurate estimate. After figuring out the materials you will need, including the total cost of everything, including labour hours, waste percentages, tax, and other costs.
- Figure out how much materials you need: It doesn't matter whether you are submitting a bid or not. Knowing how much materials you will require is vital for any project. Besides, if you underbuy these materials, you may have to spend on extra trips to bring in more materials, which eventually causes job site delays. If you overbuy the materials, you will have nothing to smile about because it will cut your profit.
Generally, with a takeoff, you will determine the materials you need and save more time and money while working on the project. A construction takeoff isn't an estimate but just the required materials for a job. They don't associate with the cost of materials needed. On the other hand, an estimation includes the costs of the materials and other additional project costs. Without a takeoff, there is no estimate.
Now that you know what a takeoff means in construction, you may wonder who performs the takeoffs. Well, the main people involved in the takeoff process are the contractors and subcontractors. They are the main deal because they are experts and qualified to determine the number of materials needed to complete a job.
However, some contractors involve estimators in this process. The estimator will take the takeoff proposal from the contractor's proposal and then assign prices to the materials listed. Remember, one of the major parts of this process is construction cost estimating.
What Information is in a Construction Takeoff
We have already mentioned that a takeoff consists of the number of materials required for the project. When writing takeoffs, there are pieces of information needed for an accurate amount and price. Ideally, there are nine main components of a construction takeoff. That is what you are going to find in this section.
- Labor expenses
- Material expenses
- Equipment costs
- Administration cost calculations
- Subcontractor cost calculations
- Overhead costs
- Contingency
- Indirect costs
- Markup or profit
Let's look at each component in detail.
- Labor Costs: Calculating labor costs includes the salaries of the workers who are part of the construction project. Those are construction workers, skilled tradespersons, project manager, and supervisors. These means you need to know the exact number of workers you will need to handle different tasks daily.
- Material Expenses: This is the cost of the materials needed for the construction project. These include raw materials such as steel, concrete, lumber, light fixtures, and plumbing fixtures.
- Equipment Costs: Equipment costs are associated with any expenses involving purchasing, renting, or operating construction equipment and machinery. This includes cranes, power tools, excavators etc.
- Administration Cost: These are procurement and site supervision costs, including coordination and project management.
- Subcontractor costs: These will include any cost associated with any specialized or subcontracted work needed for the project.
- Overhead Costs: Overhead costs include insurance, general administrative costs, permits, and project management fees.
- Contingency: It is commonly used in construction businesses and could cover unforeseen circumstances like labor strikes, weather changes, unexpected site conditions, changes in scope requirements, potential safety risks, and equipment breakdown.
- Indirect Costs: Includes expenses that are indirectly associated with the construction project, such as temporary facilities, utilities, site security, and environmental compliance.
- Markup: This is the extra amount added to a construction project's direct costs and used to determine the total selling price. Because of this, the contractor or construction company can cover the expenses and still make a profit.
How to Do Takeoffs From Drawings
Takeoff is a crucial process in the construction industry, and using it for the first time can be problematic. There are 3 ways that you can use to perform takeoffs from drawings: manually, digitally, and automated.
A few years back, there were only two main methods, but since Artificial Intelligence took over in most industries, it's now possible to automate the takeoff process using takeoff software.
Manual Takeoffs
The traditional physical blueprints and plans still stand as one of the best blueprint takeoff processes. Most construction design experts are still using it to find accurate material takeoffs.
Though you can find accurate takeoffs manually, this will depend on the estimator. The estimator must read the drawing accurately and plan for all work, including plumbing and electrical schematics and general building plans. Also, the drawings may contain some notes and symbols that may indicate the material needed, so the estimator needs to be really careful.
Manually working with this takeoff process means you will need pencils, markers, and colored pens to differentiate various items and the materials specified. This description shows that this is not just a time-consuming process; paper blueprints are also expensive.
But, if this is still your preferred takeoff process, consider using a clear plastic overlay to avoid marking the blueprint directly. Then, transfer the materials and quantities to spreadsheets to determine each component's material cost.
Even if manual takeoffs can be accurate, it has some downsides. This is a time-consuming process and needs the estimator's full attention. So, if there is a human error, you will get a bad estimate, affecting the entire process. This means manual takeoff is not ideal, especially for complex projects requiring accurate measurements.
Digital Takeoff Software
Many companies are producing digital blueprints in this modern age. If you check out online, you can come across numerous digital takeoff software. This takeoff software has been designed to streamline the takeoff process and can also partially automate it.
Though each takeoff software has a different specification, you can still analyze your blueprints and enter the required measurements and quantities in digital format. Some of these takeoff software are integrated into a bidding program, so you can combine both processes.
When you choose to use a digital takeoff process, you will definitely eliminate the downsides experienced in manual takeoffs. Considering digital takeoffs means;
- You will get up to 10x faster takeoffs as compared to manual takeoffs
- It will promote teamwork and collaboration among colleagues
- You can work from whichever location as you can access more than one device
- It will become easy to access the plans and documents because of its digital storage capabilities
Minimized manual data entry
- High level of accuracy when it comes to material takeoffs
- You can easily access the previous data for project forecasting and review
When you have access to the right digital software tools, the takeoff process becomes successful as you and your team can easily incorporate labor materials using customizable and pre-built libraries and also create a bill of materials required for suppliers.
And that's not all; you will also get insights into your construction team's schedule and performances. That is because this software offers a bid calendar in which you can tell the bid each member is working on, their workload, and their win rate. Also, you can export data from a digital takeoff platform to analyze the type of job bringing in more profits for a better long-term decision.
Automated Takeoff Software
Automated takeoff software is another construction estimating solution that improves efficiency and eliminates human error. Remember that accuracy and efficiency are crucial components in the construction industry. And this is where automated software comes in. This software streamlines the takeoff process by generating accurate material quantities.
So, how does automated software streamline material takeoff? This software uses advanced algorithms and technology to eliminate the need for manual measurements and calculations. Automated software measures material quantities from digital blueprints and PDF/CAD drawings.
The programs in this software can help you analyze and classify digital files based on textual description, identify relevant construction elements such as roofs, doors, windows, and walls, and then calculate the quantities. So, there will be no need for manual measurements.
Another thing about automated takeoff software is its digitalized measurement tools. This tool lets you measure areas, volumes, and lengths directly on your digital drawing. This ensures there is consistency and accuracy in the takeoff process.
Additionally, through automated takeoff software, you can update measurements in real-time. Whenever you make a change to the digital drawing, the software automatically recalculates the quantities and updates the data based on the information provided.
When it comes to storage, automated takeoff software offers a centralized repository for takeoff data. All the takeoff data are securely stored and easily accessed. So, it limits the risk of misplacing the paper blueprints and takeoff documents. Contractors and subcontractors can also easily use it as a reference for their future projects.
What is an Example of Construction Takeoff
Now that you understand why the takeoff process is crucial in construction projects planning, you must also know there are various types of construction takeoff.
That includes drywall takeoff, plumbing takeoff, concrete takeoff, lumber takeoff, flooring takeoff, roofing takeoff, and electrical takeoff. Let's look at a practical example of a thorough takeoff of a residential house. Mind you, in this example, you can use digital takeoff software, automated takeoff software, or just perform the takeoff manually.
You first have to conduct a blueprint analysis. Go through the architectural and engineering drawings of the residential house. Then, identify every blueprint component, such as flooring, windows, doors, roofing, walls, etc.
After that, you have to quantify the material of each component. Let's use flooring as an example. In this case, you will be performing a flooring takeoff. To do so, you will;
- Measure the shape and area of each space that needs flooring.
- Identify the type of material needed for each room, such as tile, hardwood, carpet, vinyl, etc.
- Calculate the quantity and square footage of each flooring material, including the costs, to get a complete estimate.
Do the same process for each component. Once you are done, analyze the labor and equipment needed for installation. Don't forget to include the labor hours and equipment costs such as renting, purchasing, and operation. Since our example is the flooring takeoff, to ensure accuracy, include the labor hours needed for flooring.
Here's an example of a sheet:
(source)
After quantifying the material of each component, assign cost estimations on each material component, the equipment, and labor cost. If it is a material takeoff, then information about the prefabricated materials and raw materials involved should be included. This will also include the brackets and fasteners needed in the installation of prefabricated materials.
Conclusion
The main idea here is to conduct a thorough analysis to accurately determine the material required and the associated costs, even in large scale projects. No matter the construction takeoff you use, your focus should be on accuracy.