Guaranteed Maximum Price Construction Contracts: Everything You Should Know
Written by Bridget Cooper
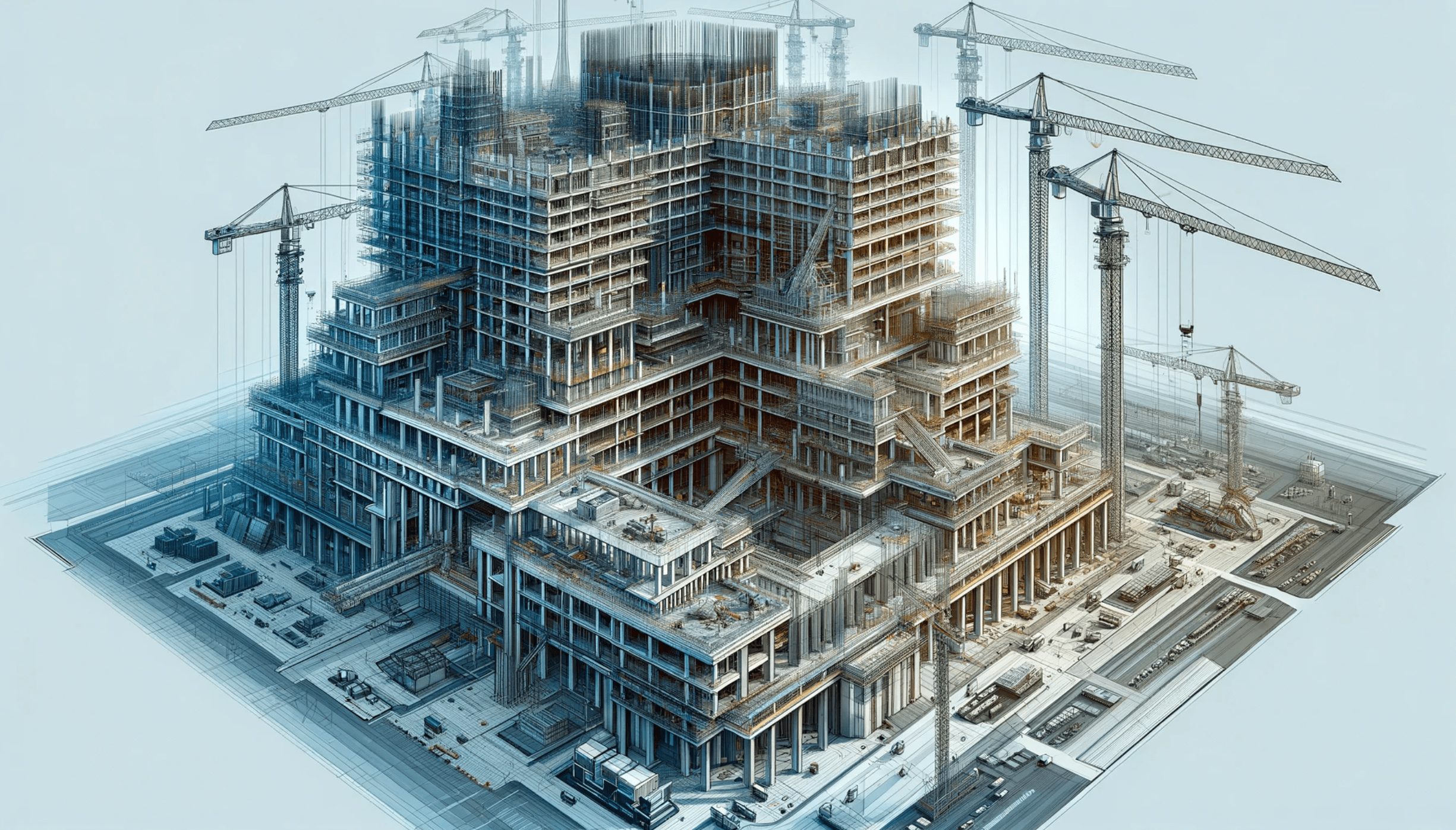
In construction contracts, the basis of all the project costs during construction depends on the pricing structure used. This is why you may have heard of pricing structures such as guaranteed maximum price, fixed price, and lump sum contracts.
Well, the most common pricing structures used for large and more complex construction projects are guaranteed maximum price (GMP) and fixed price. So, having a detailed contract structure that meets the project scope is vital, whichever method you choose.
This article will focus on guaranteed maximum-price construction contracts, their benefits, disadvantages, and differences between the two common pricing structures.
What is a GMP contract?
A GMP contract is the maximum price a construction project owner pays the general contractor on a project. Beyond that, the contractor pays for the additional costs. It is sometimes referred to as a "construction manager at risk contract."
In this construction contract, the project owners benefit more as it minimizes financial risk. In this case, the contractor has to ensure not to exceed price of the project as per the GMP contract. This construction contract term is most common in large and complex projects as the owner also tends to benefit during the upfront engineering phase.
Unlike in lump sum contracts, where contractors are paid a flat fee for the project, GMP contracts assist the owner to save more. That is, if the project costs are less than the actual costs. The contractor and project owner can also agree to share the cost savings as an incentive to the contractor.
In general, in GMP contracts, the contractor charges the owner labor costs, materials, and a contractor's fee. The total project cost can be less but not exceeding the GMP.
What Does the Guaranteed Maximum Price Contract Entail?
The guaranteed maximum price contract covers the following;
- Project Costs: These include direct costs associated with project including the contractor's profit, costs for labor, equipment, materials, and expenses.
- Contingency Amount: This is often a percentage of the GMP that the contractor can use to account for unknown and unforeseen conditions.
- General Conditions: These are the costs associated with the construction project and cannot be directly linked to the raw materials, labor, and equipment used.
- Allowances: Just as the name suggests, this is the amount set aside to cater to known unknowns related to labor, material and other costs. For example, an allowance is included to account for other line item such as such as bathroom tiles.
- Contractor Markup: This is a percentage of the total project price to account for the contractor's profit and overhead costs.
The GMP contract is so common between the owners and the general contractors. However, contractors and subcontractors are also maximizing the use of this agreement, especially on construction projects that need specialized expertise.
What are the Benefits of a GMP Contract?
A GMP contract has numerous benefits to both the owner and the contractor. If you want to be in your construction project, then you should consider the GMP contract. Here are the benefits of GMP contracts.
1. Reduced Risks
In the GMP contract, all risk shifts from owners to contractors. The risks in the bidding process involved include cost overruns and project delays which shift to the contractor. This way, the owner is protected against unexpected delays and costs.
However, the inherent risk with the GMP gives the contractor an upper hand. The contractor can charge a higher fee and defend it with greater control over the construction project and costs. After all, the contractor carries all the risks associated with the project.
2. Budget Certainty
Another interesting benefit of a GMP contract is a construction budget certainty, as the contractor handles the projects within the guaranteed maximum price. So, the chances of cost overruns are reduced in this case. Still, financing the GMP contract is much easier because the lender doesn't have to deal with any cost uncertainty.
The general contractor is the one who manages the project costs and also schedules it. Ideally, contractors have greater project control, meaning there will be minimal budget certainty.
3. Increased Transparency
GMP also offers tremendous transparency in construction projects, as the owner receives all details from the contractor. The owners are given an open book accounting to keep track of the project's actual costs as the project continues. GMP is a good example of an open book contract with transparent contractor costs.
This means that owners can question labor costs, materials, etc. Since the contractor is involved earlier in upfront engineering, they can develop a realistic GMP as they influence the design and construction method.
Since both parties want a high-end product in the end, the GMP contract makes all these mechanisms possible through a change order, we'll discuss it later in the article.
4. High-Quality Outcome
GMP is a collaborative approach in the construction industry as it involves the owner, GC, and subcontractors. All parties are involved in the decision making process, making it easier to execute a high-quality project outcome.
It's the contractor's responsibility to ensure that the construction project meets the requirements and specifications listed in the GMP contract. Since the contractor is in charge of quality control, you may get performance incentives included in some GMP contracts.
This incentive to the general contractor motivates them to work on the contract terms and encourages them to lower costs. The contractor and project owner can then split the cost savings. Additionally, since GMP is a collaborative process, the transparency and trust built between the two parties pave the way for more partnerships in the future.
In general, owners who benefit from GMP contracts are those concerned with project cost certainty without compromising on quality outcomes. For general contractors, there is a strong chance for potential savings if you develop an accurate budget and manage construction work effectively.
What Are the Disadvantages Of GMP Contracts?
Though the owner and contractor enjoy great benefits from GMP contracts, some drawbacks exist. However, these drawbacks can be avoided if a well-structured contract is established.
While using the GMP, project owners must know every detail of the construction process. This way, it will be easier for them to handle the billing, paperwork, etc. Without these details, they risk facing additional expenses like hiring a project manager to manage the project.
If the owner doesn't know how the construction process works, there is a possibility the contractor can take advantage of them. The contractor can choose to present an inflated GMP comprising low-quality materials just to increase the contractor's profit. To avoid this, it's necessary to ensure that all the drawings and specifications are detailed enough.
The GMP contracts have unforeseen and unknown conditions and all these financial obligations return to the owner. That is why we insist on having a detailed review of the specifications in the contract because not all costs are the owner's responsibility. If not, overrun costs may occur and the contractor will have to pay for it or request a change order if the GMP contract permits.
Another disadvantage of GMP construction contracts is that there is a possibility of disputes arising. The dispute may be about the project costs falling under the contract, especially for uncertain costs. Also, there can be a dispute for change orders as the contractor is the one who accounts for all project costs. If the project scope changes, a change order may cause a dispute between the two parties.
However, all these disadvantages can be avoided by using a comprehensive contract that includes price cost estimates, detailed project specifications, and mitigating the risk involved.
What is The Difference Between GMP and Fixed-Price?
The main difference between GMP and fixed price contracts is the upfront engineering and contract project cost. Below are detailed explanations of these differences.
Guaranteed Maximum Price Construction Contracts
In guaranteed maximum price contracts, there is some flexibility because there is a set maximum price GMP contract established based on a process program rather than using a construction level drawing to determine the price. The owner pays for the project costs before the project kickstarts. The construction contract includes the contractor's profit, a percentage of the overall project costs. The GMP contracts are best for companies;
- Without a clearly defined project execution method
- Who have no strong in-house engineering team
- That is still polishing up their construction process
Through the GMP contracts, such companies have much flexibility regarding upfront engineering. So, there are no budget surprises as the project goes on. However, if the prices are higher than the guaranteed maximum price, they will pay for the overages. But this can change if they submit a formal change order.
Also, a GMP contract price is usually higher than that of a fixed price or lump sum contract. That's because of the development process and the additional engineering time needed. Still, the client won't have to pay for design changes like in fixed-price contracts.
Fixed Price Contracts
The fixed-price contracts have a lower engineering cost than the GMP contract, but they are not inherently cheaper. Fixed-priced contracts have a specific price for the construction project. So, it doesn't matter whether the contractor spends more or less for the project; the estimated price remains the same.
Usually, fixed-price contracts are paid in instalments at different phases of construction. So, having all the project details before kickstarting the contract is vital. Fixed-price construction contracts are commonly used by clients;
- With a clearly defined project execution method
- Have a strong in-house engineering team
- With established construction processes
These companies have already spent some money before contracting. Their engineering team worked on the project scope before they sent the fixed-price contract. The owner or company is doing everything upfront.
This means that there will be no potential changes in the final design, just as it is done under a GMP contract. This upfront work by the owner maintains the project’s cost well below GMP. But there are times when an owner will have to modify a fixed-price contract.
That’s whenever they have other tasks beyond those defined in the project scope, with costs that were not known when making such a contract. Thus, if changes are made to the design documents, then the client must authorise an additional engineering cost change order.
The process for a change order may be outlined within the contract itself. So, project owners and contractors can request a change order whenever these changes are made. Generally, under both GMP and fixed price contracts, this very same engineering works.
However, this will depend upon clients and project costs. In fixed-price contracts, the owner finishes upfront engineering, whereas in GMP contracts, upfront engineering continues with the contractor through design or accurate project scope determination.